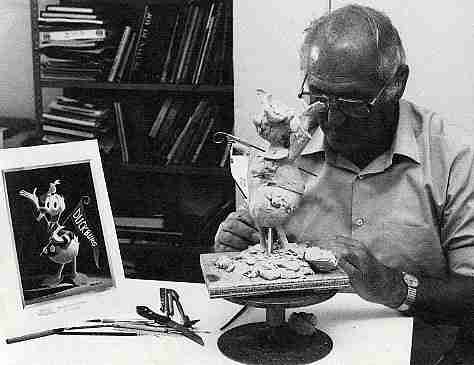
1 |
The
sculptor begins modelling a first rough figure in
plasteline. After completion it is dissected and
the parts used to create master molds. |
|
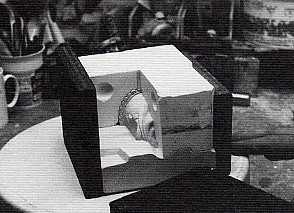
2 |
Part
of the frame is removed from the mold showing
three completed sections and the space where the
fourth will be poured. |
|
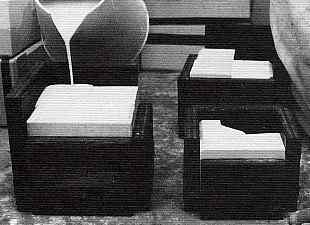
3 |
The
final sections of 3 of the molds are cast in
liquid Plaster of Paris. |
|
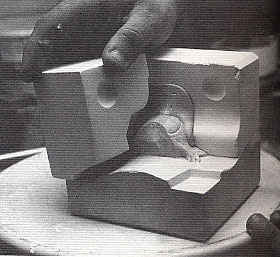
4 |
A
completed mold is taken apart and checked for
imperfections. |
|
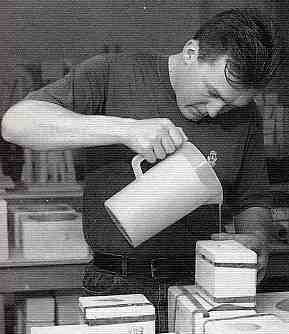
5 |
Liquid
clay is poured into each mold through a small
hole in the top. |
|
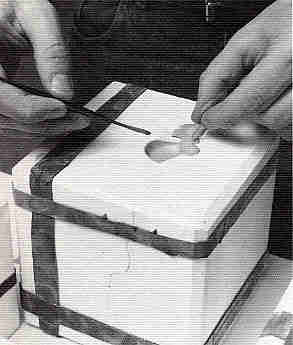
6 |
The
thickness of the cast is checked. Then the excess
clay is removed. |
|
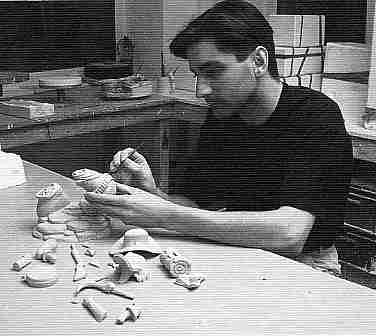
7 |
Before
the figurine is assembled, all the casting seams
are removed. |
|
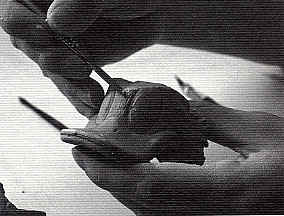
8 |
All
blurred details are meticulously sharpened by
hand. |
|
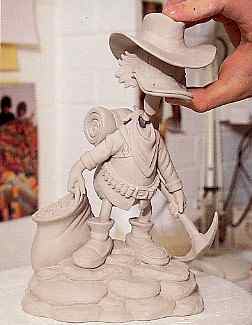
9 |
Scrooge's
head is gently positioned on his body. |
|
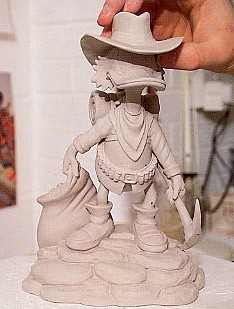
10 |
Then
it is secured with clay slip. |
|
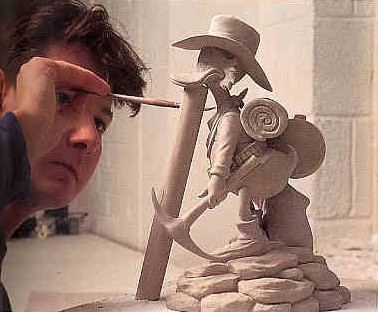
11 |
Excess
slip is removed and the figurine receives a final
touch-up. |
|
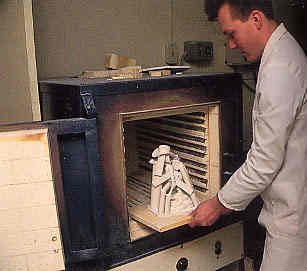
12 |
Fully
propped, the figurine enters the kiln. |
|
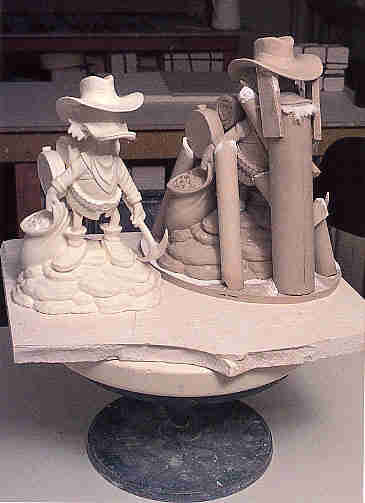
13 |
Two
figurines - after and before the kiln process. |
|
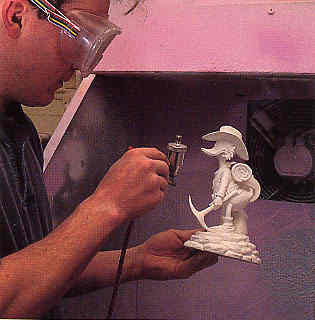
14 |
Bisques
are polished with repeated blasts of tiny glass
beads. |
|
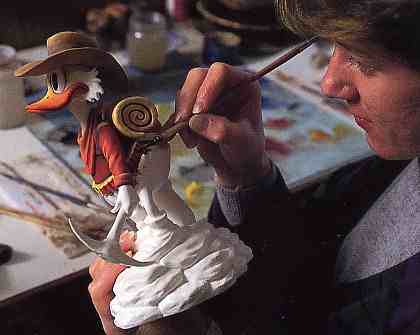
15 |
A
painter carefully applies colour to the figurine. |
|
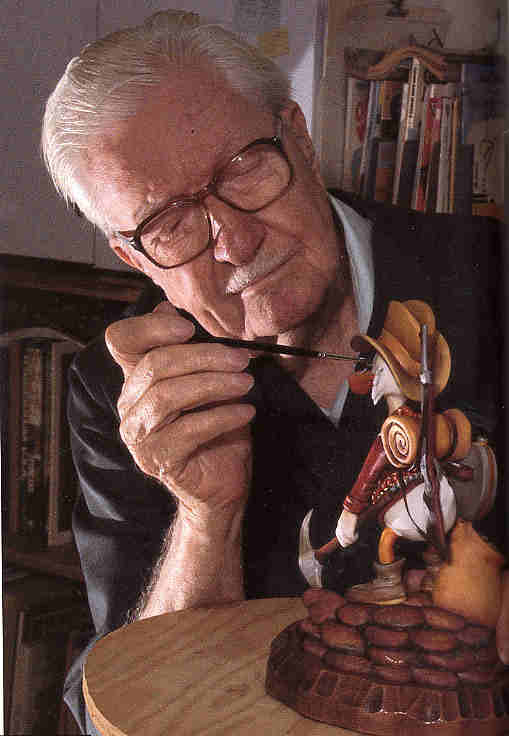
16 |
Now
Barks receives the prototype and he makes a few
corrections. |
|
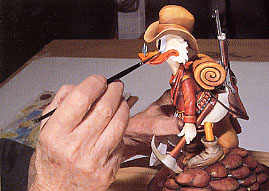
17 |
Adding
a pale blue in the eye rim to avoid a staring
effect. |
|
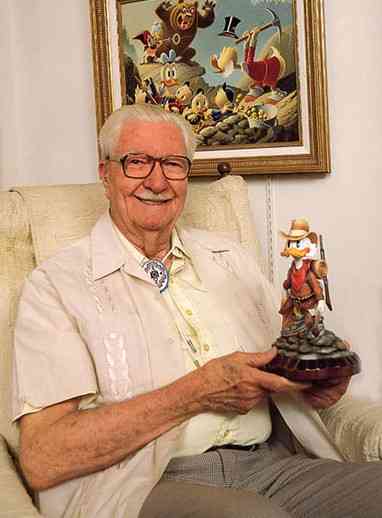
18 |
Finally,
the prototype for the figurine is ready! |
|